Using Lean principles in manufacturing is a great way to improve the quality of a product and service. Moreover, if used correctly, it will definitely improve a company’s financial performance overall.
If you are in the manufacturing industry, manage a manufacturing industry, teach employees, or would just like to learn more, then this article is for you.
In this article, we’ll briefly talk about the history and overview of Lean Manufacturing, its goals, and its pros and cons. In the final section, we’ll recommend the best Lean Manufacturing training materials and companies.
Overview and History
What is Lean Manufacturing? Lean Manufacturing is a process that allows for companies to improve processes and output.
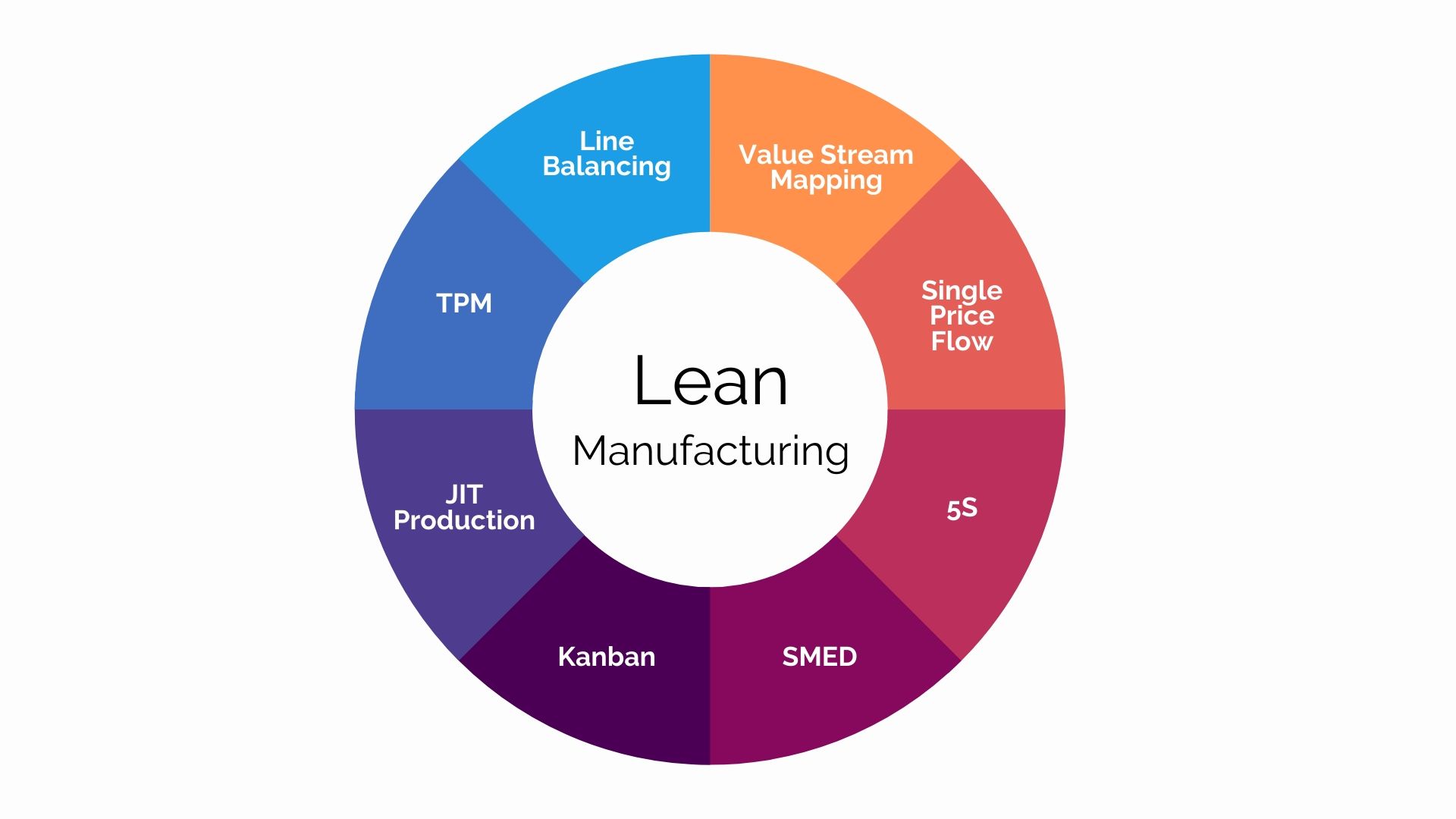
As the name suggests, a company can do this by becoming “lean”. Most people who exercise have a goal of becoming lean. This means that they are taking out anything bulky and unneeded from their bodies. This principle can also be applied to manufacturing businesses.
Thus, Lean Manufacturing reduces any waste that can affect what gives the company value. They also improve it by altering the physical layout of workplaces.
When a company’s processes are leaned out, the idea is that the output is also increased. In a manufacturing setting, this can be done by decreasing startup times and making sure that equipment works among others.
The idea of Lean Manufacturing actually came from Toyota Production Systems back in 1990. If people look back at their history, they will see that their small company started to grow at the same time that Lean Manufacturing was being applied.
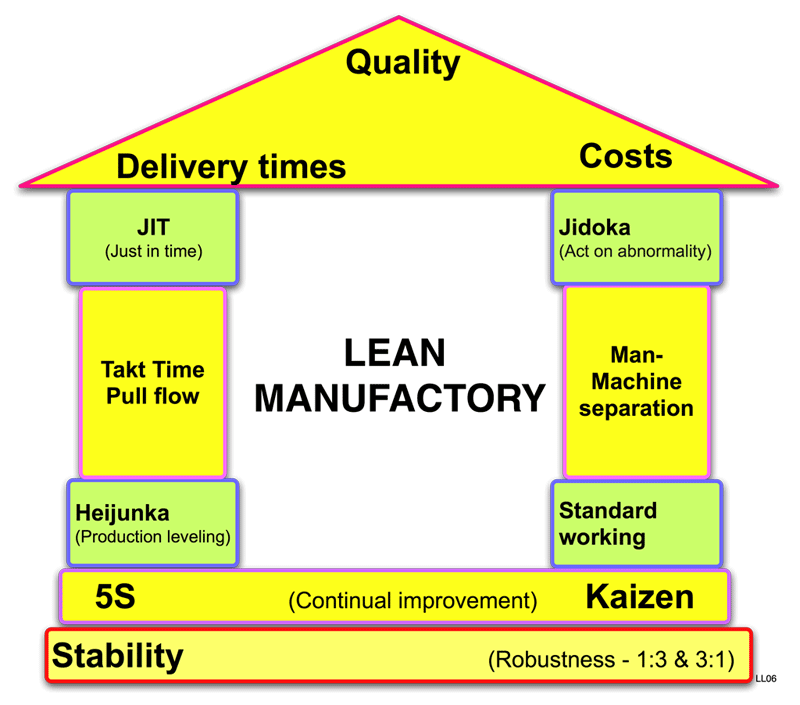
While this is the first time that the Lean principles were used in a manufacturing company, the principle was actually thought up by Benjamin Franklin. He posited that avoiding unnecessary costs would allow for a company to become more profitable.
By 1911, mechanical engineer Frederick Winslow Taylor expanded the concept even further. He added the analysis and improvement of certain processes.
Finally, in 1988, John Krafcik used the term “lean” with regards to manufacturing in his master’s thesis. He ended working for Toyota as a quality engineer.
Goals of Lean Manufacturing
Depending on who you ask, the goals of lean manufacturing may differ. There are those who say that the goal is to increase profit. Others say that the improvement in quality is to benefit the customer.
Whichever side you are on, there are several common goals that Lean Manufacturing should target.
Wasting Waste
The first goal is to take all the unnecessary and costly parts in a company. The waste needs to be taken out and shed.
For Lean Manufacturing, waste is something that takes away resources, costs, and time without adding anything of value.
Quality Improvement
Quality is another top priority. The idea is that customers have ever changing wants and needs. Thus, a company should not rest on their laurels. They should continuously strive to improve in order to keep up with the demands of the client.
One way to do so is to always strive to improve the quality of a product or service being offered.
Save on Time = Save on Cost
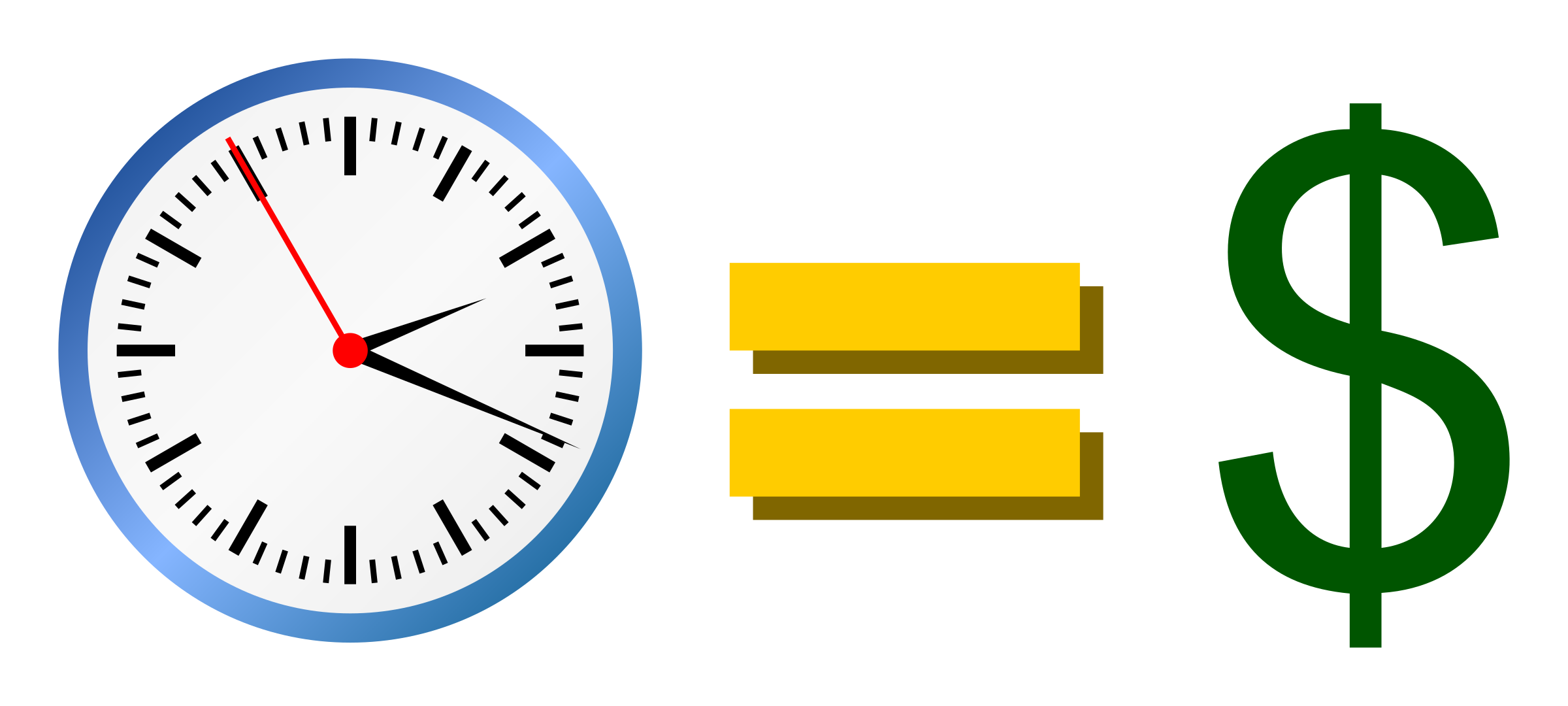
Time is one of the most important resources. It applies to all people and even businesses. The Lean Manufacturing methodology acknowledges this.
Any wasted time is a wasted opportunity for making any money. People who run and operate businesses should always strive to speed up how long it takes to finish projects. They can do this by focusing on the processes, shedding any waste, and (you guessed it) being lean.
When this is done, costs are also saved. A company that is fully productive, without any waste whatsoever, is a company that continually earns money.
This is not to say that companies should produce as much as they can. Excess production is also considered a waste. This can add to the storage fees, which add to overall costs.
Cons of Lean Manufacturing
We’ve touched upon some pros of Lean Manufacturing. These are saved time and costs. Let’s look at the other side of this coin.
The biggest boon to Lean Manufacturing is the communication aspect. If management applies this method to the company without telling any of their employees, it may cause some problems.
Not communicating Lean Manufacturing to the employees is a wasted opportunity. A wasted opportunity is of course, wasted time.
The employees are the fuel to the engine of the company. They make things go around, and they do what needs to be done for the product or service to be delivered.
As such, they have great knowledge on the multiple processes that go on within the company. Applying Lean Manufacturing without consulting them may cause the wrong types of problems to be zoned in on. The real problems may escape the scope.
Lean Manufacturing Training Materials
We hope that the explanation on Lean Manufacturing has excited you. If you are ready to learn more, these following training materials are for you.
Research Papers
First, let’s touch on some of the research papers that you can read to understand the inception of Lean Manufacturing. These can serve as the foundation for further learning.
We have actually spoken about some interesting research papers in the previous topics.
First is Benjamin Franklin’s “Way to Wealth” (1758). Franklin wrote various proverbs into this book. Each of them advocated for industry and being cost-effective.
One interesting part of the frugality aspect talks about people who don’t know how to save on costs. They will end up working their whole lives and die without a penny to their name. This is where he calls for saving as well as earning.
He indicates that people can save by taking away expensive unnecessary items. In a sense, it equates to being lean. This is a great short read.
Next up, we have Frederick Winslow Taylor’s “Principles of Scientific Management” (1909). Taylor posited that making people work as hard as they could would not improve output and productivity.
Instead, he said that focusing on how the work was done and making that efficient was the way towards positive worker productivity.
Finally, we have the most recent study; it is John Krafcik’s “Triumph of the Lean Production System” (1988).
This article is still very relevant today. An important point it presented was that a Lean Culture is not made of tools. It is the culture of a company and the management style that is applying the Lean methodology.
Training Courses
The readings are a great way to understand how the Lean process came about. It is also a good way of getting into the Spirit of Lean. However, it does little to actually teach the Lean methodology.
We’ll look at a couple of training programs available today that you can take to learn more about Lean.

First off, we have the online-based training from Quality Training Portal. It is considered a Masters-level course and will last approximately 15 hours until completion. The intended users are all employees in a manufacturing company.
The course is split up into three parts.
- Lean Concepts – The first module will teach you the basic Lean concepts. It will teach you about key terms, the concept of eliminating waste, certain components, the value stream analysis, and the Lean mindset.
- Lean Practices – In this module, you’ll be familiarized with Lean Practices that happen in the workplace. These include streamlining the value stream, workplace organization, setup reduction, TPM, visual workplace, and continuous improvement among others.
- Implementing Lean – When you’ve learned the basic terms, concepts, and practices, it is time to understand how you can implement these into your workplace. Topics include starting with people, layout options, data driven Lean, the roadmap of Lean, and even some pitfalls.
You can head to their website and even try out a free lesson. Head on over and see if this is the right course for you.
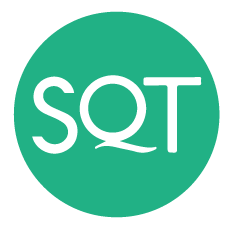
Next up, we have SQT Training’s Lean Manufacturing Tools course. It takes a total of 3 days to complete and is taught in-house.
The great thing about this course is that it is flexible. You have the ability to customize the programme that you want to take. The quotation differs for each customization.
On the regular though, there are certain topics that are generally covered. In this course, it is covered in 9 units.
- Lean Thinking. This covers the general history, overview, and principles of the Lean methodology among others.
- Takt Time and Standard Work. Takt time is the average time when a production unit starts work, all up until the next team starts production. In this unit, you’ll learn about what standard work is, the elements of standard work, determining cycle times, and making standard work efficiency by focusing on a decreased use of labor, equipment, and materials.
- Lean Material System and Kanban. A Kanban system is a ticketing system that allows people to plan and plot out work.
- Improvement Cycles. In this unit, you’ll be taught the Plan-Do-Check-Act (PDCA) improvement cycle, selecting the right improvement tools, understanding the difference between root causes, direct causes, and contributory causes, and more.
- Value Stream Mapping. A Value Stream Map is a document that shows the lifecycle of a product or service. It starts from production and ends when it reaches the customer. In this unit, you’ll understand how to create, analyze, and develop future value stream maps.
- Lean Foundations. This unit focuses a lot on Workplace Organization, 5S Workplace Organization, Total Productive Maintenance (TPM), and Overall Equipment Effectiveness.
- Single Minute Exchange of Die (SMED) System. The SMED system is the process of reducing the time for equipment changeovers. Lesser time for changeovers means less interruptions to work.
- Kaizen Events. Kaizen events are short brainstorming sessions. These sessions are focused on the improvement of certain processes. This is important for continuous improvement.
- Quality, Mistake-proofing and Line Layout. In the final unit, you will learn about how quality and Lean Manufacturing intersect.
One great thing about this training program is that you will be guided by a tutor who has spent years working in the manufacturing industry.