The 5S methodology is an organization system for workplaces used in manufacturing and other industries for decades to improve efficiency, reduce waste, and increase safety. It is also considered one foundational pillar of having a Lean company.
The 5S’s stand for the procedures that include Sort, Set in Order, Shine, Standardize, and Sustain, and each S represents a different step in the process.
In this article, we’ll provide a comprehensive guide to the 5S methodology, including what it is, how it works, and how to implement it in your workplace. Whether in manufacturing, healthcare, or any other industry, the 5S methodology can help you create a more organized, efficient, and productive workspace.
Understanding the 5S Methodology
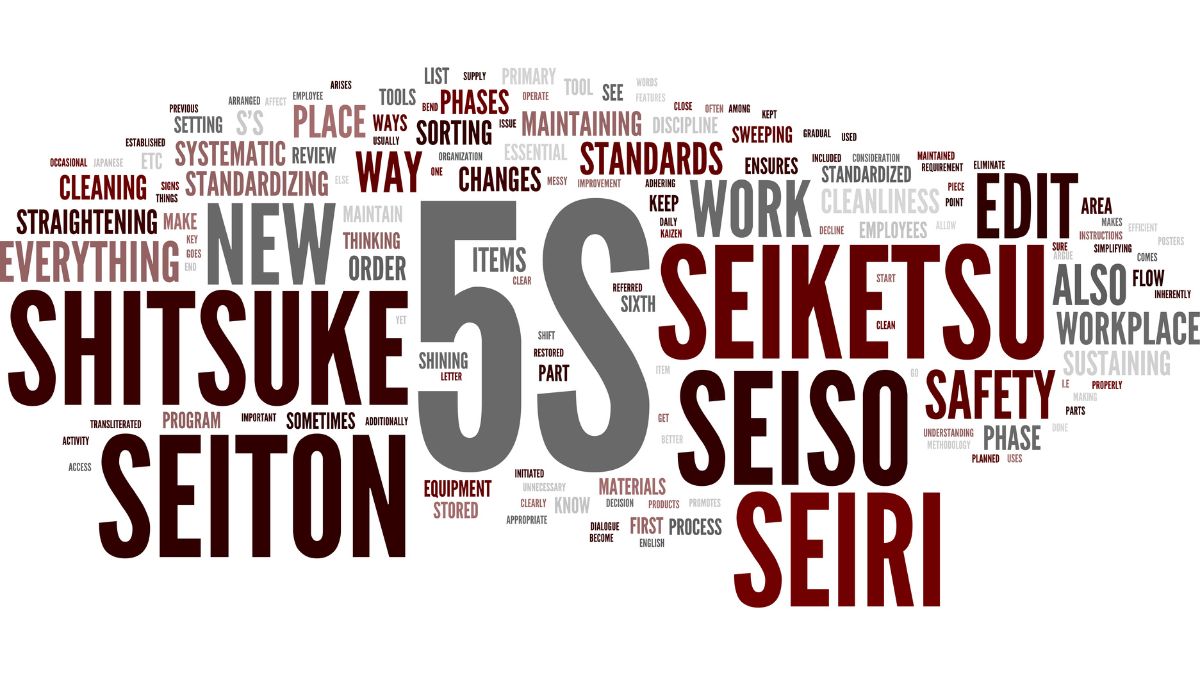
Sort
This involves going through all the items in a workspace and separating them into three categories: keep, discard, or relocate. The goal is to eliminate clutter and unnecessary items.
Set in Order
Once the workspace has been sorted, the next step is to organize the remaining items logically and efficiently. This might involve creating storage solutions, labelling items, or establishing a system for inventory management.
Shine
This involves cleaning and maintaining the workspace to ensure it is safe and functional. This might involve regular cleaning, maintenance of equipment, or establishing a cleaning schedule.
Standardize
In this step, the goal is to establish consistent procedures and practices throughout the workspace. This might involve creating standard operating procedures, establishing guidelines for how work should be done, or implementing quality control measures.
Sustain
The final step in the 5S methodology ensures that the improvements made during the first four steps are sustained over the long term. This might involve ongoing training, regular audits, or assigning responsibilities for maintaining the workspace.
By following the 5S methodology, organizations can create a more organized, efficient, and productive workspace. The following section will provide a detailed guide to implementing the 5S methods in your workplace.
Implementation of the 5S Methodology
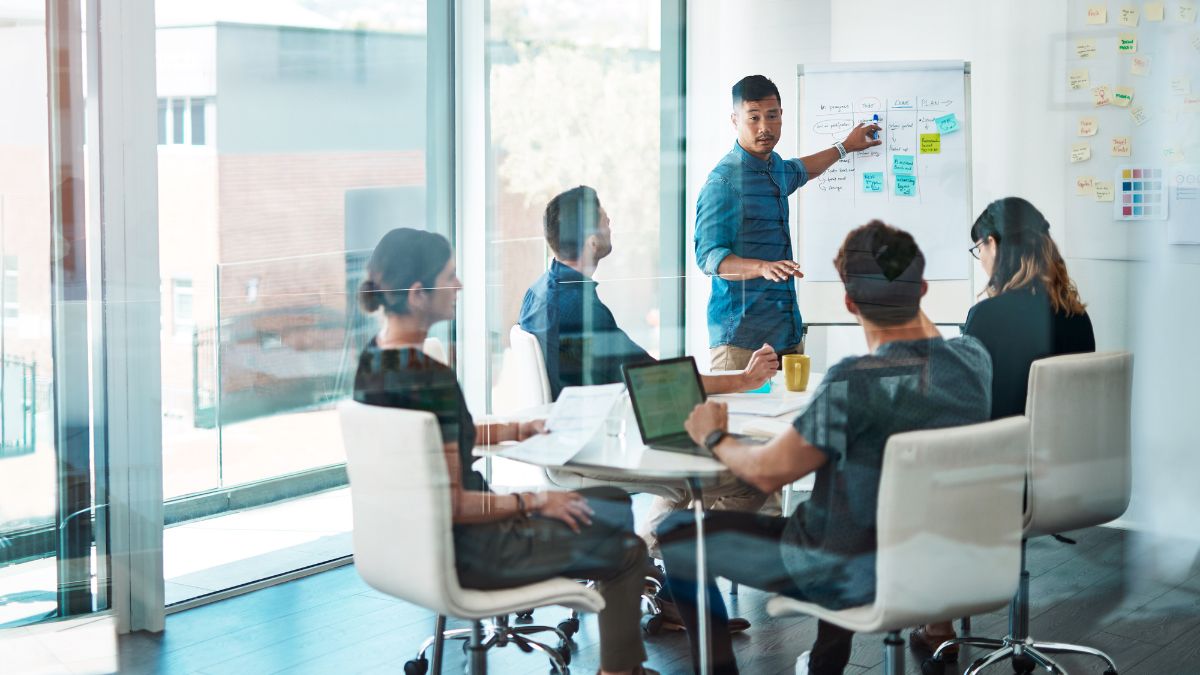
Implementing the 5S methodology in your work involves a series of steps, each building upon the previous one. Here is a step-by-step guide to implementing the 5S method.
Establish a Team
The first step in implementing the 5S methodology is establishing a team responsible for overseeing the process. This team should include representatives from all levels of the organization. Also, it must be led by someone with experience with the 5S methodology.
Conduct a Workplace Assessment
The next step is to assess the current state of the workplace. This might involve observing work processes, interviewing employees, or reviewing documents and records. The goal is to identify areas where improvements can be made.
Sort And Organize
Once the assessment is complete, the team should begin sorting and organizing the workplace. This involves going through all the items in the workspace and separating them into three categories: keep, discard, or relocate. The team should then organize the remaining items in an orderly fashion.
Clean And Maintain
With the workspace sorted and organized, the next step is to clean and maintain it. This might involve establishing a cleaning schedule, maintaining equipment, or implementing a preventive maintenance program.
Standardize
The team should establish consistent procedures and practices throughout the workspace in this step. This might involve creating standard operating procedures, establishing guidelines for how work should be done, or implementing quality control measures.
Sustain
The final step is to ensure that the improvements made during the first five steps are sustained over the long term. This might involve ongoing training, regular audits, or assigning responsibilities for maintaining the workspace.
By following these six steps, organizations can successfully implement the 5S methodology and create a more organized, efficient, and productive workspace.
Despite having the right steps in place, there is still the roadblock of getting everyone involved. Let’s take a look at several tips for getting the employees and management to buy-in and support these steps.
Additional Resources for Learning More About the 5S Methodology
Many resources are available online and offline if you’re interested in learning more about the 5S methodology. Here are a few places to start.
Books
Many books provide a detailed overview of the 5S methodology and how to implement it. Some popular titles include “5S for Operators: 5 Pillars of the Visual Workplace” by Hiroyuki Hirano and “5S for Service Organizations and Offices: A Lean Look at Improvements” by Debashis Sarkar.
Online Courses
Many organizations offer online courses and training programs focused on the 5S methodology. These can be a great way to understand the method better and learn how to implement it in your workplace.
Conferences And Workshops
Attending conferences and workshops focused on the 5S methodology can be a great way to learn from experts and network with other professionals interested in workplace organization and efficiency.
Consult With Experts
If you struggle to implement the 5S methodology in your workplace, consider consulting with an expert. Many consultants and consulting firms specialize in workplace organization and efficiency, and they can provide valuable guidance and support.
By taking advantage of these resources, you can learn more about the 5S methodology and how to implement it in your workplace.
Improving Organization, Efficiency, And Safety
The 5S methodology is a powerful tool for improving workplace organization, efficiency, and safety. By following the five steps of the 5S method – sort, organize, clean, standardize, and sustain – organizations can create a more productive and enjoyable work environment. The beautiful thing is that these steps can also be applied at home.
However, implementing the 5S methodology requires buy-in from employees and management, and ongoing support is needed to ensure the improvements are sustained over time.
If you want to implement the 5S methodology, start by conducting a workplace assessment and forming a team to oversee the process. Involve employees in the process, communicate the benefits, and provide ongoing support to ensure the improvements are sustained over the long term.
Remember that implementing the 5S methodology is an ongoing process requiring a commitment to continuous improvement. By staying focused on the end goal – a more organized, efficient, and productive workplace – and following the steps outlined in this article, you can successfully implement the 5S methodology and enjoy its many benefits.