Lean Manufacturing is a way of thinking that can be applied in any industry, but is most commonly used in the manufacturing and production industries. It is a strategic and operational method that seeks to eliminate waste and improve quality and efficiency.
By understanding what Lean Manufacturing is, you can begin to incorporate its principles into your own business or workplace for improved results.
In this guide, we will break down the history, definition, and principles of Lean Manufacturing so that you can start using this valuable methodology today.
What is Lean Manufacturing?
First, Lean Manufacturing is a method of optimizing a business’s performance and efficiency by removing any unnecessary costs. Lean Manufacturing seeks to minimize waste in all areas of a business so that they can focus on what is important: the customer.
By following Lean Manufacturing principles, you will be able to efficiently produce products or deliver services while offering higher quality than your competitors.
Two of the most common terms are “Lean Thinking” and Lean Manufacturing. Lean Thinking is an ongoing cycle that seeks to continually improve the business’s processes over time.
Lean manufacturing, on the other hand, is a specific methodology that can be implemented within Lean thinking. Lean manufacturing focuses on improving the efficiency of production and minimizing waste in order to create higher quality products with lower costs throughout each process.
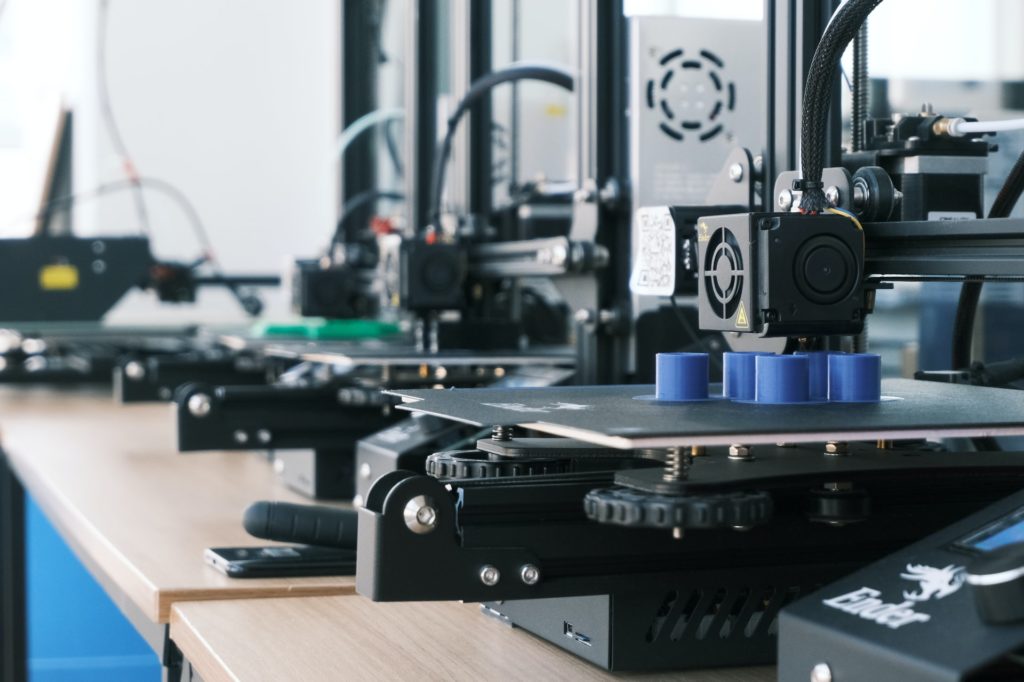
The Importance of Eliminating Waste
Lean manufacturing begins by identifying all types of waste within a product’s value stream, which includes waiting, excess inventory, over-processing, defects, and transportation before returning to the place where they originated.
Lean Manufacturing then seeks to eliminate these types of waste throughout every stage of the process until only value-added activities remain. It seeks to increase customer satisfaction through Lean Daily Habits while also increasing productivity and quality of each process.
Lean principles work to reduce transportation costs by moving materials closer to the places they are needed in Lean Manufacturing, decreasing excess inventory through Lean Management techniques, and streamlining production processes with Lean Manufacturing tools like Value Stream Mapping.
These are only a few benefits of Lean Manufacturing.

Lean Manufacturing History
The Lean philosophy was popularized in the 1980s by Taiichi Ohno, who worked at Toyota Motor Corporation. Lean Manufacturing has its roots in Japanese culture, where it originated as part of “just-in-time” (JIT) inventory practices which were put into place in post-WWII Japan in order to rebuild industry more effectively.
Lean manufacturing, in particular, was built upon many of the lean practices already used by Japanese manufacturers. Lean thinking is based on concepts that were originally developed by Toyota’s founder Sakichi Toyoda and his son Taiichi, who expanded upon the JIT principle to create Lean Manufacturing.
The general objectives of Lean include muri, mura, and muda. These are translated into improving designs to take out overburden, improving designs to take out inconsistency, and eliminating waste respectively.
Lean Manufacturing helped make Japan one of the most advanced industrial nations through its focus on eliminating waste and minimizing costs while increasing production speed.
Key Lean Manufacturing Principles
When the Lean Manufacturing principles are understood well and applied to the workplace, it creates a culture of innovation and continuous improvement. These help businesses stay current, ahead of the competition, and more importantly, successful.
Let’s take a look at several key lean manufacturing principles that practitioners need to understand and apply to their work places.
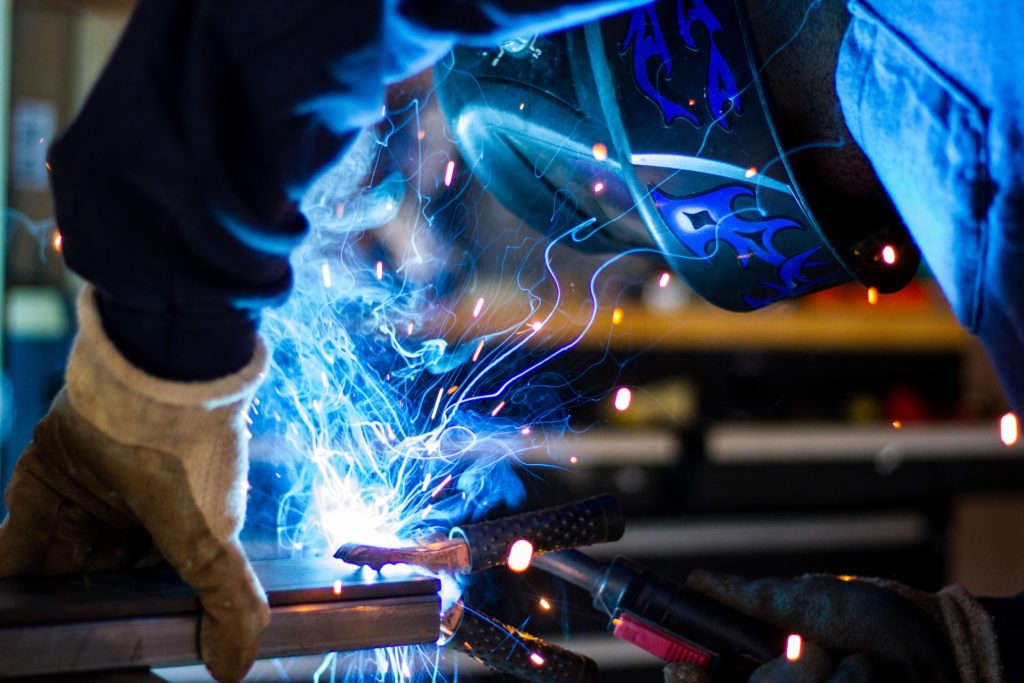
Identify Value Streams
Lean Manufacturing aims to identify what is specifically valuable about each process while removing any steps that do not add value for the consumer. Lean seeks customer input in order to understand what is important and begin removing unnecessary steps to streamline the process.
It works to identify and remove any activities that do not add value for the customer while also improving the efficiency of each process so it can be completed faster without wasted time or effort.
It also aims to reduce downtime in between processes through the aforementioned daily habit while increasing quality through principles during production.
By focusing on the things that add value only, businesses can ensure that their time, effort, and costs go to what can help them improve overall.
Knowing All the Steps
In order to properly improve the overall process of a manufacturing business, it is very important to understand all the steps that take place within the process chain.
Understanding the life cycle of a product is an important part in understanding how to efficiently produce and distribute them.
By breaking down these processes, you can identify where waste or other issues exist that could be improved upon for better results.
Optimizing Flow
Lean manufacturing is about optimizing flow. Put differently, it is all about creating a system that delivers value. This can be done via a pull-based manufacturing system.
The sustainability part of this relies on effectively managing capacity, making sure the workload is balanced and manageable throughout your whole supply chain, from production all the way to distribution or delivery.
Implementing pull manufacturing systems can help you with maintaining an efficient workforce while also ensuring sustainable performance for both consumers but most importantly employees who work there too!.
With a pull manufacturing system, inventory is only pulled through each production center when it’s needed to meet customer orders. This allows “just-in time” delivery of work which eliminates the need for an unlimited amount at once.
Doing so gives everyone a present and singular point of focus. At the same time, it helps keep overhead low as inventory is only brought in when it is needed.
This pull system can also be used for task lists, with members only taking on new tasks once older once are completed. This controlled and measured approach ensures that if changes are introduced, the team is agile enough to adapt.
The Importance of Continuous Improvement
In order to continue making improvements in products and processes, businesses must be committed to continuous improvement.
This starts at the core of what Lean manufacturing is all about. It is constant revisions for the better; an unending cycle where businesses are always looking out for various things that can be improved.
This principal must be ingrained in the culture of a business. With everyone in the company shares this principle of continuous improvement, it has the capability of making a long-lasting impact.
Measuring Metrics
In order to effectively manage anything, especially activities in the manufacturing industry, there has to be something to measure in order to see how one measures up to the success.
The importance of manufacturing metrics is essential for organizations looking to improve their performance. Lead time, cycle time and other Lean related measurements can be tracked using this data in order make sure that changes are having the desired effect on production processes without wasting resources or overworking staff members.
It’s also important not only give visibility into how things work internally but externally too where customers may have an idea what type product they want based off these numbers.
Project managers and business owners can make use of a variety of Lean project management tools to organize, oversee, and improve various facets of the process.
Learn Lean Today
Lean is a process that can be used in any industry, especially manufacturing, to improve the flow of materials and products. The goal is to reduce waste and increase efficiency.
While the concept is simple, putting it into practice can be difficult. There are many tools and techniques that can help you get started on your Lean journey.
Learn all about Lean today and get started in integrating quality improvements to your process, products, and business as a whole.