Total Productive Maintenance
Total Productive Maintenance is a holistic approach for increasing productivity by ensuring availability of the machine used in the production of goods. It empowers employees to take control of the reliability of machines by doing basic maintenance tasks like oiling, lubrication and tightening.
Jishu Hozen Definition & Meaning
Jishu Hozen is a Japanese word that means autonomous maintenance. “Jishu” loosely translated, means – independence, autonomy. “Hozen” when translated to English means – preservation, integrity or conservation.
Jishu Hozen is one of the eight pillars of Total Productive Maintenance, the other seven being:
- Focussed Improvement
- Planned Maintenance
- Training & Education
- Early Management
- Quality Maintenance
- Safety, Health & Environment
- TPM in the Office
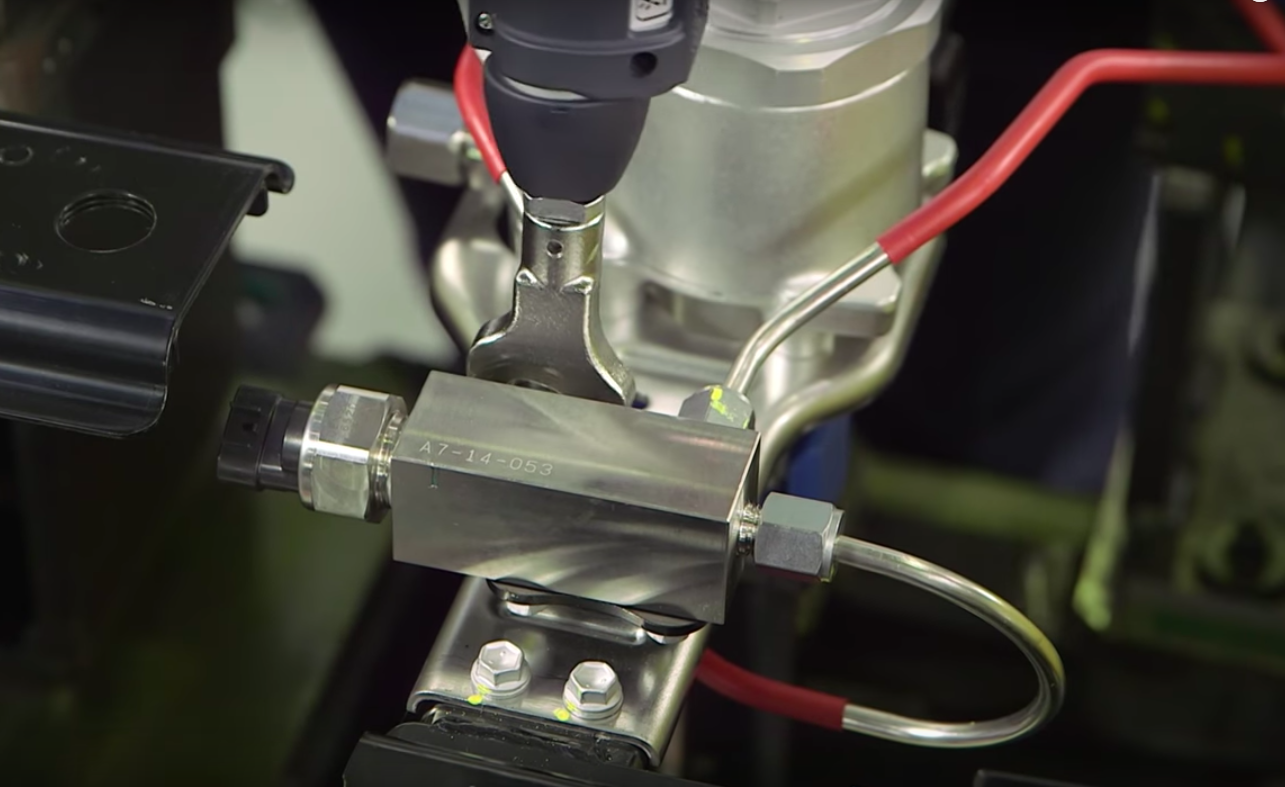
Objectives of Jishu Hozen (Autonomous Maintenance)
The main objective of Jishu Hozen is to empower the employee to make a daily conscious effort to maintain the performance of equipment and processes.
In a normal operational setup, employees are usually classified into various categories including operators and technical staff.
When such a categorization is made, employees will tend to stick to their assigned roles and will not do anything beyond the scope of their job description.
For example, if the machine an operator is working on stops functioning, he will simply call the maintenance staff to fix it without even bothering to find out what went wrong. This is despite the operator is constantly using the machine and probably knows more about it than even the technical staff.
Autonomous maintenance aims at reducing such complacency by empowering the employees to take responsibility of certain basic aspects of machine maintenance such as cleaning, lubrication and inspection.
These basic maintenance steps goes a long way in enhancing machine life and capacity, leaving the more thorough maintenance to technical staff.
The following are the main objectives of an autonomous maintenance program:
- Check the deterioration of machines
- Keep machines/ equipment working at their optimal performance
- Return equipment to their original condition
- Prevent machines from failing
- Increase the skill levels of the operators
- Prevent quality defects
- Improve profitability
How does Jishu Hozen prevent machine deterioration?
When a machine or any other equipment is manufactured, there is a predetermined life-span beyond which it starts performing below expectations.
The reduction in performance over time occurs due various factors including misuse. The major categories of machine deterioration are:
- Natural deterioration – this is the expected life-span of the machine that the manufacturers have designed into it based on tests carried out in their research laboratories
- Forced deterioration is the reduction in the functionality of machines due to improper usage by operators
As these conditions continue to manifest themselves, a decision has to be reached on whether to decommission the machines and replace them with newer ones. The capital costs of replacing non-performing machines are usually high and these replacements usually take a long time to materialise.
It becomes necessary therefore to develop a system of maintenance that keeps machines in good working condition for a long time. The total productive maintenance program aims at keeping machines well maintained, with a higher availability for production and less downtime.
This unnatural deterioration is called forced or accelerated deterioration and can be caused by a variety of factors such as wrong usage, lack of maintenance and environmental conditions.
To mitigate against such deterioration, the autonomous maintenance program must address the causes by establishing the basic condition of the machine through activities such as cleaning, lubricating, tightening and oiling.
Autonomous maintenance addresses natural deterioration by trying as much as much as possible to extend the life of the machine beyond its nameplate lifespan.
Corrective maintenance of the machines by increasing the operational conditions, safety, maintainability, reliability and quality of repair ultimately increases the lifespan of the machine.
Importance Preventive maintenance in Jishu Hozen
Preventive maintenance of machines can be likened to a person taking precautions so as not to fall ill.
It is a daily program of carrying-out maintenance, inspecting for abnormalities and addressing them at the earliest stage possible before they become bigger than they already are.
Daily maintenance prevents deterioration through activities such as lubrication, cleaning and adjusting loose nuts and bolts.
The machine has also to be measured regularly to determine the degree of deterioration through inspection checklists.
Any signs of increased deterioration are then systematically addressed so as to prevent them from becoming bigger than they already are which will be costly to repair.
When such problems are left to get out of hand, there is also the likelihood that the machine might have to be scrapped and replaced with a new one.
Preventive maintenance is therefore a very important part of the autonomous maintenance program because it has positive implications on quality, cost and delivery to the customer if done in the proper manner.
Machine Ranking Sheet Sample
Machine Name
|
Cost
|
CRITICAL (YES/NO)
|
RANK
|
---|---|---|---|
NCC
|
$10000
|
YES
|
1
|
ICE MAKER
|
$5250
|
YES
|
2
|
CONVEYOR
|
$6500
|
NO
|
3
|
Target for Total Productive Maintenance
The main target for TPM is improve on the metrics listed below:
- Overall Equipment Efficiency – or OEE is a measure of how effective a piece of equipment vis a vis the availability and productivity. When the machine has a high OEE it means that there is very little downtime and it is producing according to the customer demand
- Autonomous Maintenance (Jishu Hozen) – the ability of machines to be easily maintained by operator level staff. When autnomuous maintenance is evident, the technical staff only come in for periodic and schedule maintenance because breakdowns are very rare
- Quality– the ability of a machine to produce as per customer specification without defective parts means that the cost of production and lost business is low and profitability per part is high
- Cost – should be very low due to low downtime and high productivity coupled with high quality
- Delivery -when the equipment is able to produce all the parts as per the customer demand it means that on-time delivery to the customer can be guaranteed
- Safety – properly maintained machines with safety features ensure that accidents are minimised or eliminated altogether
- Multi-skilled workers are able to man more than one machine and therefore can be better utilised to realise the goals of production
Initial Steps of Total Productive Maintenance (TPM)
To begin the Total Productive Maintenance program requires a schedule of activities in order to ensure that gains are sustainable in the long run. The following are the bare minimum requirements for the successful implementation of a TPM program:
- Top Management decision to begin program and provide the necessary resources
- Establishment of cross-functional teams which draws its members from across the value stream. This mixing of team members from many departments makes cooperation easier during the normal operations as members get to have broader understanding of each other’s work
- Defining targets narrows the scope of the program and gives team members a way of knowing the progress of their efforts
- Drawing master plan for the program gives a clear road map of the direction the organisation should take
Calculating OEE
Overall Equipment Effectiveness is a measure developed by Seiichi Nakajima in the 1960s to evaluate the effectiveness of manufacturing utilisation.
OEE= AvailabilityXQualityXProductivity
TPM Pillars
A sound TPM program is anchored on the following six programs:
- Autonomous Maintenance
- Continual Improvement
- Planned Maintenance
- Quality Improvement
- Training
- Office
- Occupational Safety, Health and Environment