There are always multiple ways to get things done. Cleaners have various recipes and techniques to make things pristine. People can lose weight through exercise or diets. And businesses can attain success via a number of processes or strategies as well.
One of those methodologies is called Lean, which focuses on the value flow to the customers. Lean focuses on factors that contribute the most value to the company and customers as well.
There are a couple of tenets that Lean follows. The first one is the idea of continuous improvement. Even if processes improve via the Lean methodology, there is always room for more improvement down the line.
The second one is respect for people. People play important roles in businesses, and their input should be respected and added into the improvement process.
Benefits of Going Lean
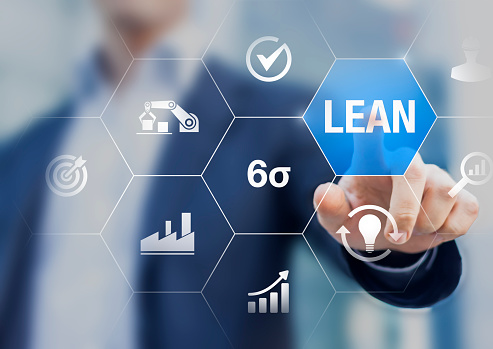
Now apart from approaching and ensuring success, the Lean methodology has a slew of other benefits as well.
For starters, the wasteful actions that Lean takes care of will allow for a more focused workforce. This isn’t just a focus on their tasks, but on things that contribute great benefit to a facility’s success.
With that said though, Lean also has a positive effect on productivity and efficiency. With more focus being put on actions of value, unimportant tasks can be thrown by the wayside, with more energy placed on better tasks.
Lean also helps to improve the various processes in a product’s lifecycle. This is largely due to the fact that Lean changes things up by ensuring a “pull system”. This system makes it so that products are only created when there is a present demand.
Finally, every facility can also save some money by saving on resources. The fact that a lifecycle only moves when an order for a product is placed, then a facility can hold on to valuable resources until they are needed. This also means that resources aren’t just wasted easily by only using them when they need to be.
There are a ton of resources out there that you can utilize in order to learn more about the Lean methodology. It is a truly effective system that many businesses and facilities are finding success with.
One interesting question that constantly needs to be revisited for all practitioners of the Lean methodology is how do you know if your facility is truly lean?
How to Know if your Facility is Truly Lean?
Too Much Inventory
Take a good long walk around your facility. Do you see large amounts of inventory in storage or surrounding areas?
If the answer is yes, then this is a telltale sign that the facility isn’t really lean. Too much inventory is a classic sign that indicates that the Lean process just isn’t working.
Too much inventory can often get in the way of streamlined processes. It also affects the “just-in-time” manufacturing process. All in all, if these are happening, it is negatively affecting the customer’s experience.
Material Flows
Another good sign to see if your facility is Lean or not is by tracking the flow of materials. Lean methodologies will store the various materials and tools near where they are needed to be used.
If the materials need to travel from point A to point B in the middle of a process, this usually takes away significant time that could be used for more value-adding activities.
Everyone is On Board
If a facility is truly applying the Lean principles and methodologies, then everyone should be on board. Once Lean has been applied to the facility, take a good long walk around and talk to the people. Try and discover who are the people who know what the Lean plan is and who don’t.
A truly successful Lean system is one that is used in each and every day of operations. Furthermore, it should incorporate all the different departments, as well all employees.
If only a select group of employees have been included in the Lean methodology, then your facility isn’t truly Lean.
Now this doesn’t just apply to employees. The management should be just as invested and knowledgeable about the Lean process as anyone else there.
Part of Company Culture
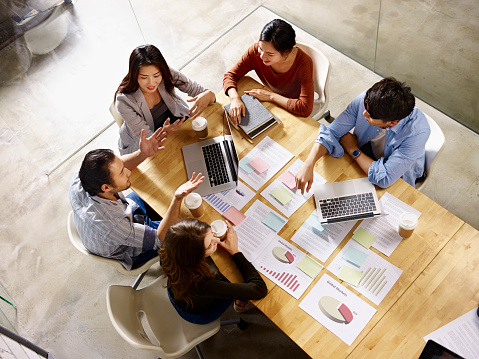
Lean is meant to be something that is truly integrated in the both the day-to-day operations and culture of the company. It isn’t meant to be treated as a series of steps towards a goal, or a project that helps get closer to a goal.
Instead, Lean is a transformative system that improves various processes, takes away wastes from the facility, and focuses on the value-adding tasks that a facility has.
If Lean is just some series of tasks that fade into the background of a facility’s process, then your facility may not be truly Lean.
Lacking Visibility
Most companies or facilities only report on projects to certain team members. It acts as a sort of “need to know” basis. However, the fact that Lean incorporates all departments and employees means that this approach simply can’t stand.
If project reporting is only done to certain people, or even when a project is just completed, then it creates a big information black hole. People aren’t in the know and could miss moments where they could’ve helped out with.
Visibility throughout the company gives the opportunity for everyone to see progress, help out in overcoming obstacles and challenges, and contribute more towards success.
Sharing Successes and Failures
Jumping off from the previous point, there is also a culture in companies and factories wherein projects are not reported if they are not successful. The fact of the matter is that projects will succeed and fail.
No matter the result, these projects need to be reported on in multiple phases. The reporting not only gets everyone on the same page. It also allows for the recognition of people’s efforts, the learning of various lessons, and the cooperation on various issues for improvement.
Worth Starting Over
Lean is a powerful and effective tool that many facilities are utilizing. Companies like Nike, Intel, Toyota, and many others have used the Lean principles to focus on the actions that give the greatest value to customers. In doing so, they have also ensured the success of their own companies.
With Lean being so effective, if you have gone about applying Lean to your facility before and it falling short, then it is always worthwhile to start over and ensure that it is applied correctly.
Lean is a continuous process that requires constant vigilance and checking. Use the various tips above to see whether your facility is truly Lean. Ensuring that the Lean methodologies are applied correctly is a worthwhile endeavor.
You might also wanna check the Top Benefits That Lean Manufacturing Can Provide Businesses.