The pandemic has hit all countries from around the globe. Not only has the pandemic affected people’s lives and health, but it has also affected the economies of various countries.
The delicate balance and business framework that has been steadily built has been smashed, like a boat amidst raucous waves. A prime example of this is with China.
China was the central hub for manufacturing and factories. It was common practice to send out the manufacturing side of certain businesses to China due to the appealing cost. However, their place at the center of the supply chain is now questionable.
Various countries have decided to take their manufacturing out of China and back to their shores. It is nothing short of a reshoring initiative. Whether it be Japan or the USA, countries are beginning to look at bringing their manufacturing back to local hands.
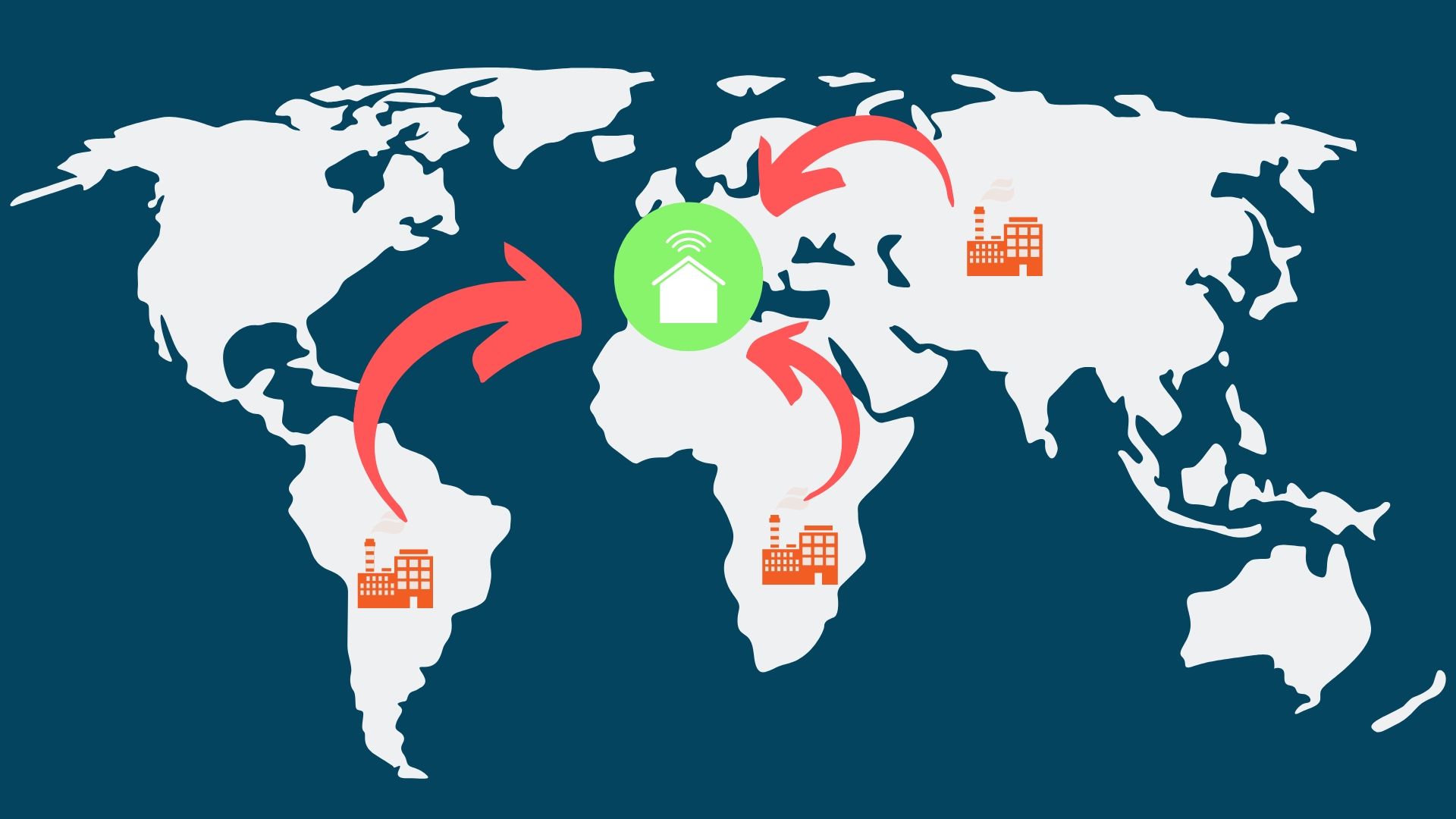
The first question is, what is a reshoring initiative? And how would a business owner best handle it?
The Reshoring Initiative
The Reshoring Initiative was presented by Harry Moser, a veteran of the manufacturing industry. Years ago, he created an organization that focused on bringing manufacturing jobs back to the USA.
The initial practice was to offshore certain jobs to certain countries. Business owners and CEOs once thought that this move was saving on certain costs. They found out that this isn’t the case. Even prior to the pandemic, wages in China started to rise.
Eventually, it was discovered that bringing manufacturing jobs to local hands could save more costs than initially thought. Moser’s organization has been helping educate the manufacturing industry on why this is the best move.
In 2016, a report prepared by Moser showed that reshoring manufacturing back to the USA added more than 70,000 jobs back to the market. Since 2010, the total number of manufacturing jobs returned is more than 300,000.
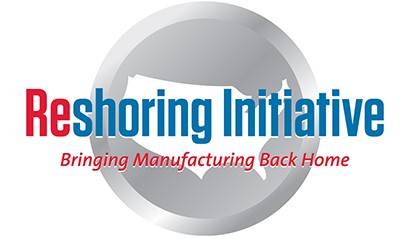
By 2017, the Trump administration is in full force for reshoring. The number of reshored manufacturing jobs per month in 2017 were at an all-time high. Apart from that, big companies like Apple, GM, and Softbank all decided to reshore.
Walmart also had a USD $250 billion manufacturing program that brought back a quarter of a million jobs.
Now that the initial wave of the pandemic has passed, certain US companies are starting up again and reshoring.
Intel – a giant in the digital world – is in talks with the Department of Defense. They are talking about improving the sourcing of microelectronics and other related technologies domestically.
Ford, General Motors, and various other automotive companies are also restarting their factories. Even Ericsson’s Smart Factory is starting up in Texas, with professionals trained via virtual reality prior to the opening.
While we have talked about saving costs, reshoring has many other benefits as well. Let’s take a look at some of them.
Positive Publicity
Reshoring improves the publicity of retailer sponsors.
Retailers can bring in more domestic products rather than imports. There is also an opportunity to increase the number of products that are “Made in the USA”. Company’s can use the reshoring initiative to document this move.
The Reshoring Initiative organization also provides advice to companies on how to promote and sell items that are made locally.
The biggest benefit would be the opportunity to participate and promote reshoring case studies. These all translate to good public relations. Other companies and even countries will be able to see the positive effects of reshoring, with certain companies in the spotlight.
Let’s look back at Walmart as a case study on good publicity in action.
Walmart is the largest US retailer. They are also the largest retailer to support the Reshoring Initiative. When they announced their support for reshoring, they also announced that they would increase their American-made purchases by USD $50 billion by 2023.
This move was not only a big publicity move for the Reshoring Initiative, but also for Walmart.
Certain labor parties were heavily critical of Walmart’s reliance on offshoring jobs. However, when Walmart came out as the lead supporters for the Reshoring Initiative, it acted as a public relation turn around for them.
Control of the Supply Chain
Another benefit of reshoring is that companies would be able to control their supply chain better.
We can look no further than Apple as a good example of supply chain control.
Initially, Apple always relied on certain Asian countries for certain parts of their operations. They had Japan produce displays, South Korea was making memory chips, and China was putting everything together.
However, this approach is problematic because Apple cannot control certain political forces that arise. Back then, the Korean peninsula was unstable. China is locked in trade disputes with the US.
Reshoring allows Apple to avoid all of these potential problems.
A Promise of Quality
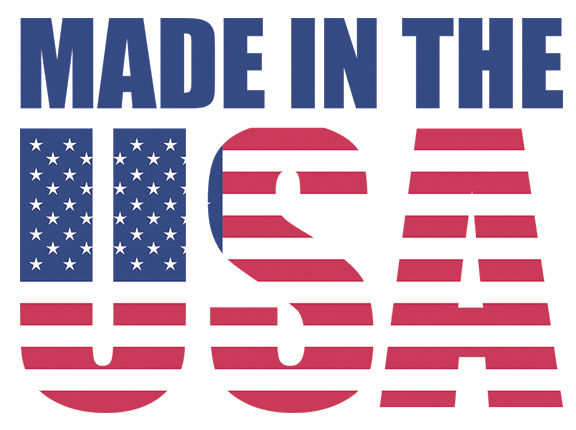
The final advantage of reshoring is the promise of quality. Companies live and die by their reputation. If products or services are good, chances are that customers will return.
Apart from that, a product or service that is “Made from the USA” elicits a feeling of respect and exudes a reputation of quality.
Our case here is Amway. Amway has a nutrition line that is very popular in Asia. This is because the USA has certain quality and safety standards that the Asian countries hold to high regard.
Just In Time
If you are a part of the factories reopening or reshoring initiatives happening recently, one important tool you can use is the Just-In-Time (JIT) Inventory Management system.
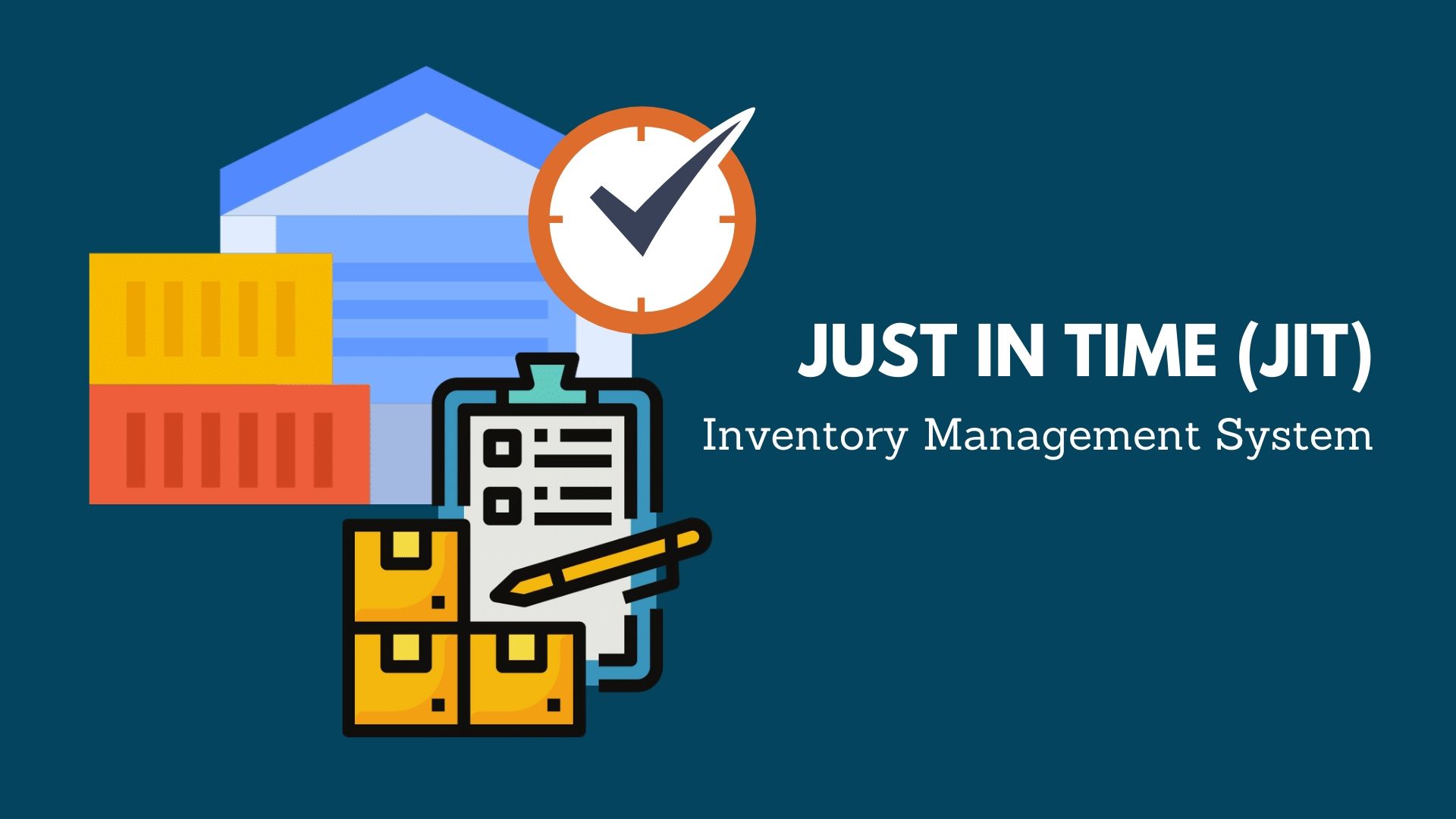
This is a system that aligns raw material orders from suppliers with the production schedules. JIT is used to improve the efficiency and decrease the waste of a company. Doing so will mean that goods are only received when they are needed in the production process.
This also means that inventory costs are significantly cut.
In order to have the JIT system work, a good amount of accurate forecasting is required.
Let’s take a look at the JIT in action. Any company that runs the JIT method needs to operate at low levels of inventory. However, they need to have a trusted and tight relationship with their supply chain. Success depends on it.
The supply chain must come through and deliver the goods when the need arises. The manufacturing company must only request for certain goods when an order is ready to be built. The order must come first.
Apart from forecasting, manufacturing companies must also have a steady stream of production, trusted and reliable suppliers, close to no errors with machinery, and quality workmanship.
The only disadvantage of the JIT method is that when one part of the process breaks down, it can have serious ramifications to the business.
If, for example, the supplier is not able to deliver the needed part at the needed time, the whole production process is at a standstill. This would then interfere with the client’s expected timeline for the product.
Several big companies are already on-board with the JIT method.
Apple
Apple CEO Tim Cook said that inventory is an evil thing to have. He says to liken inventory to milk. If it is kept too long, it becomes a problem for the company.
This is why Apple decided to lessen their inventory on hand. They avoided overstocking parts and products that could become obsolete.
Zara
Zara is another company that uses the JIT method. They can be described as a “fast fashion” company. The fact that they control their own supply chain means that they can bring certain items to market whenever they want.
Similar to Apple, Zara also believes that inventory is “death”. By the start of the season, only 50% of its clothing line is decided on. The other half is manufactured in the middle of the season.
This strategy allows for Zara to react if any designs or styles become popular in the middle of the season. They act fast and get these hot items to the stores immediately.
Tesla
Finally, we have Elon Musk’s Tesla. Tesla’s growth throughout the past months has been monumental. However, they are still a relatively small automotive company. As such, they cannot enjoy the same things that big car manufacturers do.
Despite that though, they rival many other car manufacturers by their supply chain. They have been vocal about opposing traditional franchise-dealer sales models.
By following the JIT method, they keep very little inventory and produce only when needed. This means that they pose very little risk to their capital and they don’t risk ending up with so much excess inventory.
Furthermore, Tesla has capitalized the long manufacturing times. They have allowed for client’s to customize their cars. This way, the client’s give way for longer manufacturing at the expense of customized builds.