Throughout our articles, we have been talking about multiple techniques and strategies for lean practices in manufacturing. The question for this article is, how does one measure the performance?
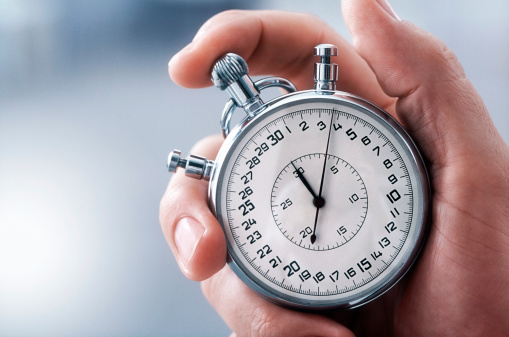
This is where cycle time and throughput come into play. These closely related measures are very closely related to each other, but have some distinct differences.
Understanding both concepts will allow you to improve performances, from managers all the way to supervisors.
Cycle Time
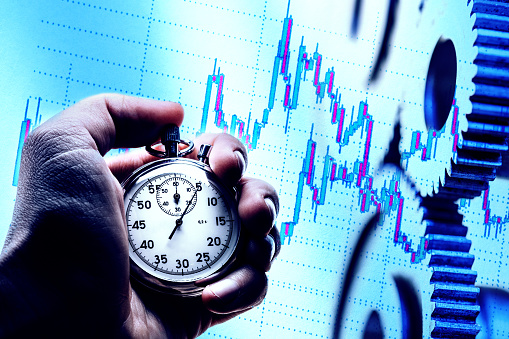
Cycle time is defined as the time that is needed to complete one full cycle of production, processes, or operations from start to finish. This can be applied from the completion of a product, to filling out forms, or even answering phone calls.
Studying the cycle time of processes will allow you to measure how efficient a manufacturing operation is.
Taking the definition of cycle time and how it was explained, we can easily deduce the elements needed to come up with it. In order to come up with cycle time, all you need is the total number of goods produced and the total time it took to produce it.
The simple equation you can use is the net production time divided by the unites produced (net production time/units produced).

As an example, if your team takes 20 hours for 200 units (20/200), that means that one cycle is equivalent to 6 minutes. This is your cycle time.
Throughput
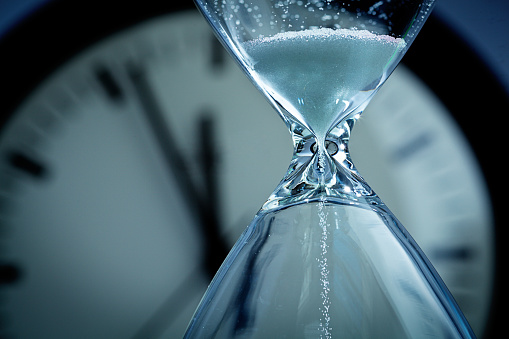
Throughput on the other hand is the time it takes a product to pass through certain manufacturing processes. It may sound similar to cycle time, but it is a bit different.
The difference is that while cycle time measures the time from start to finish, throughput measures the time within each manufacturing process or step, from when it starts manufacturing until it exits.
The throughput time includes several intervals. These include:
- The processing interval – This is the time when raw materials are transformed into a finished product.
- The inspection interval – This is the time when materials, certain processes, and finished goods are checked on.
- The move interval – This is the time when materials are moved in and out of manufacturing areas, and even between workstations.
- The queue interval – This is the time spent waiting in between the other intervals.
In order to calculate your throughput time, the formula is similar to cycle time. It is the sum of all above interval times over the units produced.
Improving Cycle Time and Throughput
The key to improving both cycle time and throughput is to eliminate waste. Eliminate tasks or lulls in work that do not contribute to the overall value of the product or company.
Improving Cycle Time
- Look at Travel Times
One easy way to improve cycle time is look at the travel times within each process. If people are walking from place to place for certain tasks for example, this is a huge waste of opportunity to have time spent on actions that can add value.
Group certain processes that have the most travel time in a common area. This will significantly reduce travel times.
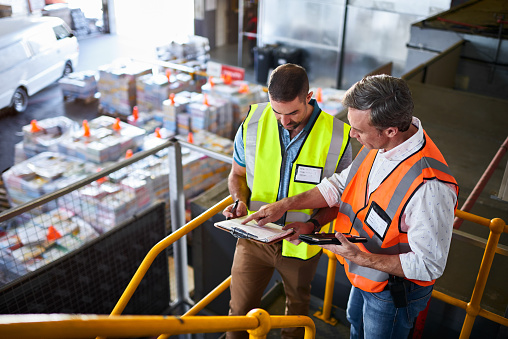
- Focus on What is Important
Another tip is to focus your resources on activities that are the most active or have the most activities.
This relates to the first tip as well. When the business grows, new processes and departments open up. Adjust where these processes and resources are placed near the areas where they will be used.
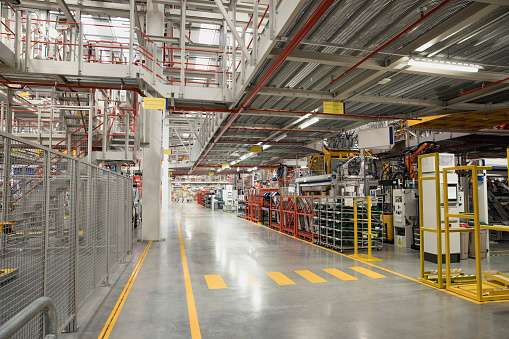
Improving Throughput
- Improve the Workflow
The first step to improving throughput is by understanding the general workflow. It all starts by understanding the processes included in your manufacturing and how they operate.
Focus on understanding if you have skilled labor for your product, if your equipment is in good condition and if it can handle what needs to be done, and if the process is clear and does not create any bottlenecks or roadblocks.

- Regular Equipment Maintenance
Another good tip is to ensure that your equipment is regularly maintained. If a vital piece of equipment breaks down, this can have the manufacturing process grow longer than expected. It can lead to inefficiencies and wasted opportunities for profit.
Be proactive. Schedule your maintenance instead of waiting for your equipment to break down. It may cost some money, but the wasted opportunity will inevitably cost more.
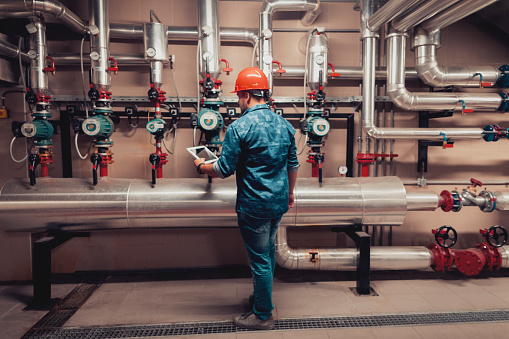
You might also wanna check Top Lean Logistics Principles.