All businesses and business owners desire one thing: success. For many, this is by increasing revenue. Different people have different ideas on how to do this. However, one often overlooked thing is by eliminating waste.
With less waste, products and services can be delivered faster and more efficiently.
This is the crux of Lean Logistics principles or lean manufacturing. It is a business model that people can follow to eliminate unnecessary actions or “waste” from their company activities. The result is quality products delivered quickly and with efficiency.
Another way to look at it is that it is a philosophy for manufacturing production that looks at how the company allocates its resources. The target is to make sure that the resources are focused on things that will give the most value for the company and the customers. In order to do this, businesses need to analyze their activities and eliminate the waste.
If you’d like to learn more, we’ve got you covered. Stick around as we discuss the following topics:
- Defining Lean Logistics
- Addressing Wastes in Logistics Chains
- Top Lean Logistics Principles
Defining Lean Logistics
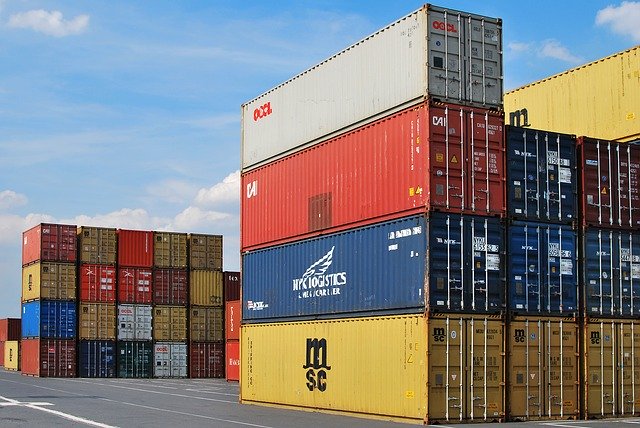
What is Lean Logistics?
The idea of thinking lean in a company actually originated in Japan in the late 80s. The definition then is no different than the definition today: eliminate waste and maximize value for the company and customers.
This philosophy is really for the logistics arm of a company. Apart from reducing the waste, the other goals of being lean are to increase the speed and flow of products. In other words, it is the faster development of products.
Lean logistics is not something that can only be implemented in one department of a company. The truth is that Lean Logistics aims to improve the overall performance of a company. When reducing company waste though, this is very important for controlling the supply chain.
Thus, the overall improvement of a company using Lean Logistics is done by improving teamwork, optimizing product management, and mastering cross-functional operations.
Benefits of Lean Logistics
One strong benefit of lean logistics is in inventory management. The lean philosophy is also applied to a company’s inventory. This means that companies don’t stockpile a large number of items in their inventory.
Instead, stocks are kept on a “as needed” basis. Too much inventory is a waste of money. However, if there aren’t enough items in the inventory, this may also cause delays for customers. Companies need to analyze and see how much items are right for a lean inventory.
The inventory is only replenished when a need arises.
Another benefit of Lean Logistics is that it analyzes the various processes and removes them. This means that process life cycles are made more efficient and faster, getting the product faster to the customer with less effort from the company.
First Steps on Implementing Lean Logistics
The first thing that companies should do when implementing Lean Logistics is identifying the different processes in the life cycle. Afterwards, the company should also identify the key roles included in each process.
Get all of these people together and examine the life cycle. This is your opportunity to identify a more ideal set of processes, with the goal of eliminating unneeded steps that don’t add any value.
Once you see what you have to eliminate, figure out how you can remove them. Analyze your improved processes, see how you can improve and optimize them further, then repeat. There must be a continuous improvement in your operations.
Addressing Wastes in Logistics Chains
The original Lean Logistics from the Toyota Production System targeted three types of deviations. These are called Muda, Mura, and Muri.
Muda
Muda is what we have been talking about so far. It points to waste in a company. A rough translation of it is uselessness. Addressing the Muda in a company means identifying the processes that do not add value.
However, there is a distinction that must be made. There are two types of Mudas. Muda 1 are activities that do not add any value but are necessary. These include things like quality assurance and control, as well as testing the product’s safety.
While these processes do not add value, they are necessary.
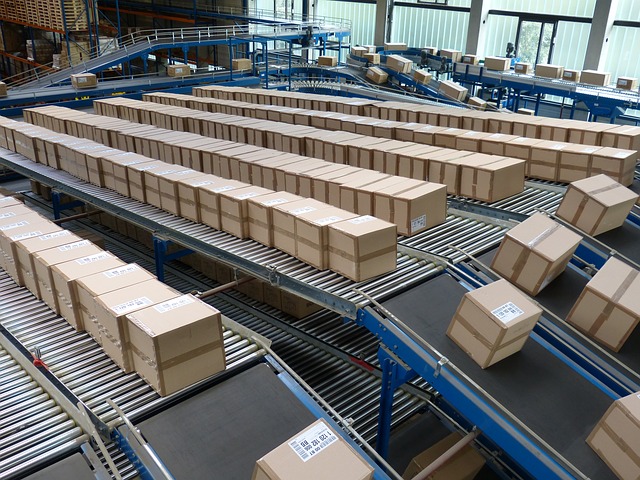
Muda 2 activities are those that need to be eliminated. The abbreviation for the types of wasteful Muda 2 activities is TIMWOOD.
- Transportation – an excess of product movement
- Inventory – Too much raw items in the inventory
- Motion – Too much movement in machines or people
- Waiting – Waiting for raw materials or customer, or work to be finished by one station
- Overproduction – Developing too many products without anyone buying
- Over-processing – Too much actions or work done by employees than what is required by the customer
- Defects – Shipping defective products that will ultimately come back to the company
Mura
Mura is translated as unevenness or irregularity. If Mura occurs, it can lead to Muri which we will discuss later.
One example of Mura is when through the life cycle of a product, the work is not evenly distributed. This means that one station does more work than the others. Thus, there would be a roadblock in one station leading to waiting and overproduction.
The goal of addressing Mura is to even out the work throughout all the stations that the product passes through.
These problems can be addressed by implementing an essential lean manufacturing tool, Kanban for a “just in time” manufacturing system. Like the lean inventory discussed earlier, a just in time system allows for inventories to be stocked only when the need arises.
These can restrict excess inventories and overproduction.
Muri
Finally comes Muri, which is translated to overburden. As the translation suggests, this happens when something is too much or unreasonable to do. This can be the workload or the production of a specific product.
This has been seen in multiple companies when people work over their 100% capacity just to get the job done. If this continues, it may affect an employee’s health and morale.
The solution for this borrows from Mura. An evenly distributed and fair workload is just the trick for eliminating Muri.
Top Lean Logistics Principles
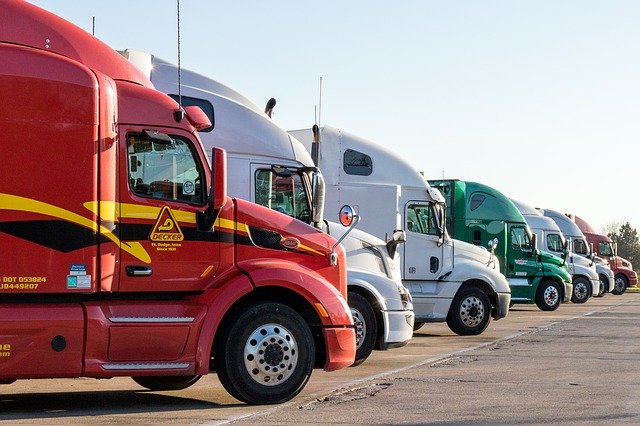
Up until this point, we have spoken about several facets of Lean Logistics. However, when using this in a company, it is very important to understand the top Lean Logistics Principles that drives the system. There are 5 in all.
1. Determining Value
The first is determining value. For this, our main touchpoint is the customer. We have to understand what the customer wants. If they don’t want it, chances are they won’t pay for it. If they won’t pay for it, it does not present any value in the product.
2. Understanding the Steps in the Process Chain
It is the responsibility of everybody in the company to break down the various steps that comprise a product’s life cycle. Once they are separated into individual steps, it will be easier to eliminate waste and improve the overall process. This is where you can apply the TPM and Six Sigma Basics.
3. Improving the Process Flow
When a company understands the overall process flow, they can first and foremost see how to improve it. Afterwards, it will also be easier to monitor the process and ensure that things are done right.
4. The Customer’s Pull
Companies have to rely on the customer’s pull. By this, we mean that products should be made for the customer’s needs. A company should not create a product and hope that customers buy it. Rather, they should understand what customers need and aim to deliver that instead.
5. Reach for Perfection
In reality, perfection is not achievable. However, it is always good to aim for perfection. With perfection in a company’s crosshairs, this will steer their actions towards continuously and consistently improving. This can be through actions, machines, processes, and more.
Ever Upward
We have come to the end of our Lean Logistics discussion. We have discussed Lean Logistics, Addressing Wastes in the Supply Chain, and the Top Lean Logistics Principles.
We hope that all of these tools can help your company improve its performance. And, as the final principle states, perfection should always be aimed for.