Throughout our journey through Lean Manufacturing, we have come across several of the top manufacturing tools that you can use to eliminate waste, improve your system, and maximize profit.
One such tool or method is Just-in-Time manufacturing. It is an inventory management principle, originating from Japan, that makes it so a company only produces products that are needed. It does away with producing excess or unneeded products. It is based upon the orders of the customers.
As the name suggests, the resources are delivered just as you need them; no more, no less.
It is a very useful and effective manufacturing tool. One way to consistently achieve it is via the Kanban method.
The Kanban Method
Kanban is a visual workflow management system for any work that follows a process. It imagines the whole workflow process, as well as the actual work as it goes through each step of the process.
The objective of the Kanban method is to eliminate any roadblocks that may hinder all the other steps from taking place and any work being finished. It ultimately tries to improve the cost, as well as the overall speed at which the process takes place.
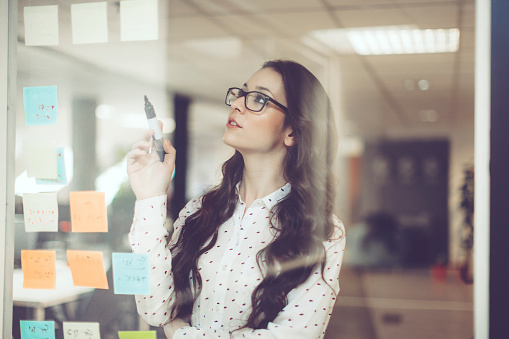
The word “Kanban” roughly means “billboard”. That in itself doesn’t mean quite much. However, it also means the available capacity for work. If you put these definitions together, it becomes the visualization of work processes on a board.
Within the board, there are a variety of swimlanes or columns if you will. The headings in each column pertain to the state of each task. Here are the four headers.
BACKLOGS |
TO DO |
WORK IN PROGRESS |
DONE |
Task example |
Task example |
Task example |
Task example |
Task example |
Task example |
Task example |
Task example |
The Backlog items are acknowledged as needing to be done, but are the least priority as of now. The To Do items are those that are a step up in terms of priority. You are essentially creating a queue of tasks.
Work in Progress tasks are those that are currently being done by the team. Finally, the Done tasks are those that the team has completed.
If you can imagine, the tasks flow from left to right. The task cards or post-its change swimlanes depending on the state they are in until they get to done.
For JIT, Kanban can serve as an important visual reminder and signal. The Kanban visual helps companies see what needs to be done, effectively pushing or being the catalyst for actions to take place. In short, it categorizes and pushes the action.
The way Kanban was developed makes it a very fitting tool for JIT, like a hand in a snug glove. It’s very nature as a visual indicator can immediately let the supply chain that demand for a product is coming.
However, it is important to note that Kanban is not just a tool for manufacturing. It has come a long way since its inception back in 1940. Nowadays, Kanban can be used for any industry, with IT being a frequent user of this method.
The Four Core Principles of Kanban
Kanban has four core principles that, when understood, can be applied to any and all workplace or process.
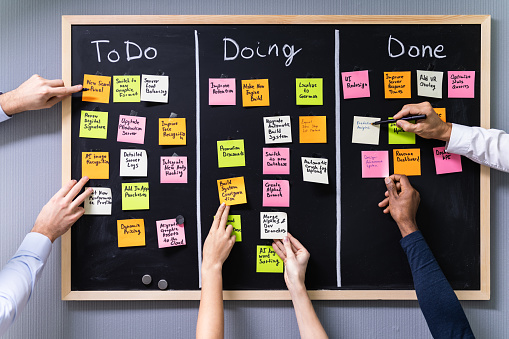
Create a Visual Model of Your Work and Workflow
The first core principle of Kanban is creating a visual model of your work and workflow. This pertains to understanding and visualizing each step in your company’s workflow.
As such, Kanban doesn’t really have a strict method for it. If you are coming in at the middle, you simply continue on with what your company’s workflow is and visualize it. You can do this on a physical board (like a whiteboard) or through various electronic tools available now.
The board that you create will allow you to see the various steps your company is going through to create the output.
If it is a physical board, you can opt to use post-it notes or index cards of varying colors. The change in color could help signify the different work types or classes of service. If there are many classes, you can create different swimlanes or columns to separate them from one another.
For beginners though, a single swimlane will do. Afterwards, you can change the board as you see fit.
Reduction of Product Under Work in Progress
The next principle is reducing or limiting the tasks and work under the Work in Progress swimlane. The idea here is to keep the number of tasks small, so the team can focus on them first before taking on new tasks.
Focus on the current Work in Progress tasks and only take on new ones when they have been shifted to the Done swimlane. This creates a sense of capacity for the team, setting a boundary of how much a team can do.
Deciding on the capacity is something that is unique to each team. You can even start off without any limits, and start building the limit once you go through a number of tasks.
Another benefit of doing this is that it also communicates to the stakeholders or customers that the team has a limit of what they can do. Thus, it serves as a warning and they need to be careful about what they ask the team to do.
Be Workflow-Focused
Once the two core principles have been applied, it will create a sense of flow. Observing the Kanban board will show you how the tasks move, the limit of tasks, and if there are any improvements that can be done.
Focus on the workflow with your Kanban. Use the data there to see how fast the tasks are getting to the end swimlane. Faster is better, but ensure that quality work is still being done.
Look out for any improvements. There may be roadblocks that are hindering more tasks from being accommodated. This is something that must be addressed to ensure a smooth flow of tasks.
Embrace a Culture of Continuous Improvement
Kanban is an on-going process, with improvements done in little steps. It improves via small steps, with improvements happening at a very steady space.
As such, it will continue to improve the more you use it. In order for improvements to occur though, you need to embrace the culture of continuous improvement. Be patient and trust in the process. Commit to Kanban and whenever you see a problem, address it.
There may be times where you don’t see an apparent problem. In these times, you can use the scientific method to improve the workflow. Come up with an improvement, set a hypothesis, test it, and get feedback if it is successful or not. Rinse and repeat.
Perfection is not attainable, but setting your sights toward it can push any team to continuously improve.
Start a Kanban Board Now
Kanban has many benefits when applied correctly. It not only gives an accurate picture of a company’s workflow, it also helps in molding into an efficient and productive one. The goal is to deliver continuous and consistent results.
Apart from that, it helps the team by limiting the number of tasks they need to do at any one time. This helps them focus more while lessening the chances of burnout.
This is why companies like Microsoft, Pixar, and Spotify all use Kanban. Now, you can too. There are a variety of online tools out there that can help you out. For starters, you can try out the free Kanban tool Trello now.
You might also wanna check Six Big Losses: Important Concepts to Always Bear in Mind.