Lean Factories is committed to sharing essential information that is important for lean manufacturing and methodology.
We have previously spoken about the Eight Pillars of Total Productive Maintenance (TPM) and Overall Equipment Effectiveness (OEE). Both of these concepts and methodologies have to do with equipment and how efficient and effective they are.
Both TPM and OEE share a goal. This goal is to eliminate what we are called the Six Big Losses. Let’s take a look at these Six Big Losses, how to eliminate them, and why it is important to do so.
Origins of the Six

The Six Big Losses concept came from TPM creator Seiichi Nakajima. He developed it during his time in Japan’s Institute of Plant Maintenance in 1971.
For Nakajima, he was convinced that maintenance is a responsibility that is shared by all employees. He figured that maintenance was best done via small group activities. The eventual goal was to increase the overall efficiency and effectiveness of each machine.
Many other methodologies we have discussed look at productivity loss through the lens of a variety of factors. These include things like the process flow, people, and other factors that organizations can eliminate waste from.
The Six Big Losses is similar in that account. It was created to identify and categorize how a business encounters productivity loss from the perspective of the equipment that the company uses.
It works hand in hand with OEE, as it provides more detail on equipment loss. Furthermore, it also provides data that can be used for actionable information for equipment loss. It is a key tool to improving a company or a business.
Understanding the Six
With history out of the way, let’s turn our attention to The Six Big Losses themselves. It consists of:
- Equipment Failure
- Setup and Adjustments
- Idling and Minor Stops
- Reduced Speed
- Process Defects
- Reduced Yield
Let’s take a look and define each.
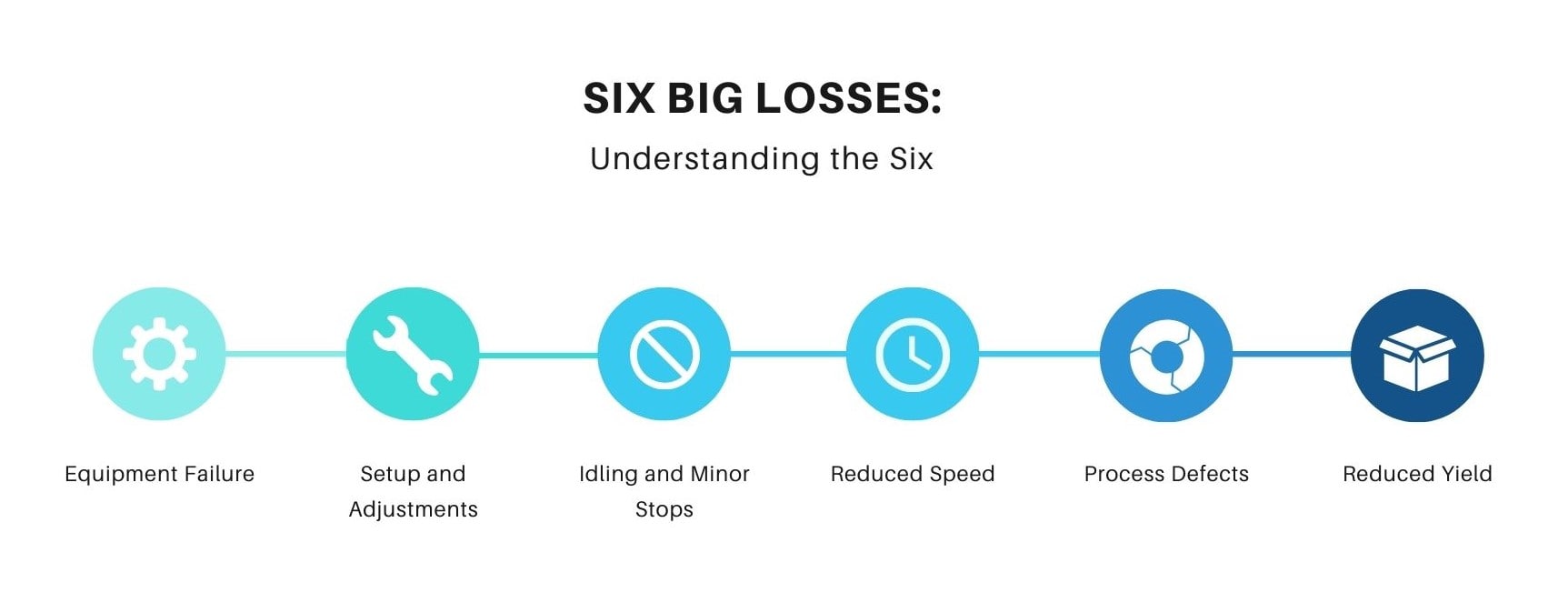
Equipment Failure
The definition of equipment failure is when a piece of equipment is meant to be up and running for production at a certain time, but is not due to some failure. If a piece of equipment has any unplanned stops, this is equipment failure.
Taking from one of the three OEE losses, equipment failure is equal to an availability loss. If an availability score is 100%, then that means that the process or piece of equipment is running at all times when it is planned to.
Thus, equipment failure takes away from the availability score, which means production time is lost. Many companies see equipment failure as the biggest reason for missed production time.
There are many reasons for equipment failure. It could be breakdowns, unplanned maintenance time, and even people not being present to operate the equipment.
A good way to solve equipment failures is to get to the root of the problem. Companies must understand what the real problems and problems are that create equipment failure.
When you associate a reason to an equipment failure assign a code, number, or classification to it. This is called a Reason Code. These reason codes will allow you to easily apply Root Cause Analysis (RCA) to these reasons.
When you are writing your reasons, ensure that the language is clear so that it cannot be misconstrued for other reasons. In addition, make sure that the symptoms are described clearly. A good bank of 25 reasons is sufficient to start with.
Setup and Adjustments
The next big loss on the list is setup and adjustments. This refers to any period when a machine or equipment is being prepped or readied. It can be times where there is a setup or adjustment period, or even when certain machines are being fine-tuned before production.
There is a debate whether or not planned maintenance is included in this loss. We’d recommend that it be added to the list, as the maintenance takes production time away all the same. However, it is only maintenance occurring during planned production time.
In order to counteract this, a business or company needs to delve back into their policies and ensure that it is consistent. Document all policies and ensure that employees follow it consistently.
With regards to setup time, companies can utilize Single-Minute Exchange of Dies or SMED. It is a set of steps that companies can follow that will cut down the setup time, ensuring more production time is carried out.
The overall goal is to ensure that setup times are reduced to less than 10 minutes (thus the “single-minute”).
This is done by analyzing each step of the setup. After documenting each step will need to be either separated (in a different process before or after the setup), converted (changed to be before or after the setup), or streamlined (made faster to save on time).
Idling and Minor Stops
At first glance, idling and minor stops looks exactly like equipment failure. However, there is a difference between the two. Idling and Minor Stops, as the name suggests, are when pieces of equipment stop for only a short time. The threshold is a couple of minutes to no more than five.
This loss is typically resolved by the operator. These include things like jams, misconfigured settings, quick cleaning actions, and misfeeds.
The ironic problem with this big loss is how small or minor it is. It usually happens each day, albeit with different problems popping up. The fact that it has become a common occurrence means that employees don’t see how it affects the company. The company also doesn’t properly track this loss.
Counteract this big loss by scheduling preventive maintenance ahead of time. Companies can also utilize 5S: Sort, Set Standardize, Shine, and Sustain. Also ensure that materials used for maintenance and in the equipment are of quality.
Another good way around this is standardization. Do away with any sort of variations to the processes being done. This can be done for the settings being applied as well as the materials being used.
Reduced Speed
Reduced Speed is when a piece of equipment is not in sync with the ideal time to manufacture a certain item or product. It is also referred to as Slow Cycles.
This often happens when a piece of equipment is not lubricated correctly, has old parts, is dirty, an operator with little experience, and prolonged startup and shutdown times.
In order to solve the reduced speed loss, the team must observe the processes and look for patterns that are occurring. Specifically, look for patterns that yield production loss. These can be at a certain shift time or maybe after a part or materials has been changed.
When these patterns have been identified, you can now apply a RCA to identify the culprits and fix them. If a fix has occurred, make sure to add any and relevant information to your standardized work procedures.
The solution for idling and minor stops can also be applied, namely doing away with variations.
Process Defects and Reduced Yield
For the last two big losses, we’ll lump them in together. While their definitions vary, the solutions are applicable to both.
This pertains to when a process is yielding defective parts during stable or steady-state production. If a part is scrapped or needs rework done, it is included with process defects.
This takes place due to operator error and wrong equipment settings.
Reduced yield on the other hand takes place during the startup and warm up times. Thus, it is taking place prior to steady-state production is reached.
Variation plays a part with these two again. Ensure that equipment settings and materials have little to no variations. Keep things standard.
Bear the Six Big Losses in Mind
The Six Big Losses is an important concept that manufacturing companies need to remember. It works well with OEE.
In general, the six big losses help to categorize the losses that pertain to pieces of equipment. The six big losses can serve to provide more important information relating to OEE. More importantly, it serves as a basis for deciding on solutions or actions to take to solve these equipment problems.