LEAN’s main goal is to minimize waste and maximize productivity. We have covered many different techniques that can help do this. These include Shingo, TPM, and even the Six Big Losses.
One of the pillars of LEAN is addressing the swift changeover of equipment. If the changeover time is quick, this means that downtime decreases drastically for improved efficiency. This is important, as downtime is a big waste that must be minimized or done away with.
Thus, we go to Single-Minute Exchange of Dies or SMED.
What is SMED?
SMED is a system that aims to transform equipment setups and changeover actions to single minute (less than 10) operations. These can be applied to almost any piece of equipment or operation.
Apart from lessening time for setups and changeovers, it will also ultimately lessen the costs of a company and grant versatility and flexibility within a process.
It was created in the 1950s by Shigeo Shingo. While working at Toyota, he noticed certain inefficiencies taking place within the body molding process. At the time, the changeover happened in a range of 2 to 8 hours.
He noticed that the waste was occurring when employees were switching and preparing new tools when the processes flowed from one to another.
This was when Shingo proposed SMED.
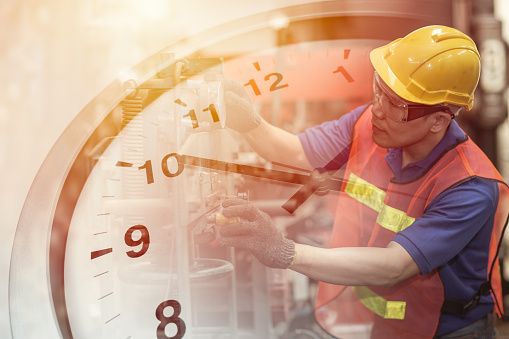
Toyota then changed the equipment in their factory, the parts of the vehicles, and even reorganizing the steps when creating car body moldings. Then, 20 years later, Toyota now has a changeover time of just 3 minutes.
If you can imagine, SMED lends well to just-in-time manufacturing. The time saved means that the product is delivered quicker by the business.
SMED Principles
Many people saw the improvements that Toyota had enacted and wanted to emulate it. Now, thanks to SMED being adapted, it has been applied to any and all sorts of processes and machineries. It can apply to manufacturing, software development, restaurant management, and more.
The principles of SMED happen in two setup components: external and internal.
External Components of SMED
External setup components or steps take place when a process is taking place or when a piece of equipment is operating. Internal setup components or steps are those that happen when neither a piece of equipment or process is running or are stopped.
When zoning on external components, these typically have to do with having the right tools or equipment at hand when a changeover is about to take place. It aims to ensure that everything needed is already available, instead of preparing them when it is time.
An example of this is a restaurant. Suppose that a restaurant has a different menu or preferred meals for breakfast and lunch. When noon comes around, it is best if the restaurant already has the choice ingredients at hand, rather than going around and looking to get these ingredients.
Internal Components of SMED
For internal components on the other hand, it is a careful examination of the steps in the process. The goal here is to see which of the steps can be changed from internal to external.
Let’s take the same example of the restaurant. Lunch time is swiftly rolling along with each and every hand tick. Now, it would be best that the ingredients needed are already ready at the chef’s side when the time comes to prepare the lunch dishes.
This is opposed to getting all the ingredients out of the refrigerator and storage right when they are needed. It is done beforehand. Thus, this is the change from internal to external. It significantly speeds up the process.
How to Implement SMED
Now let’s take a look at a series of steps that will help you implement SMED.

Step 1 – Choose and Identify a Process
The first step is to choose and identify a process where you want to improve the changeover times. Here are some criteria to help you decide on a process:
- The changeover time is quite long and can be improved upon
- There have been a lot of different changeover times for a specific step
- The step or process happens regularly
- The employees are knowledgeable and trained in the process. Furthermore, they are in favor of the improvement and change
- The process is important in the overall operation, wherein it may cause delays for other steps
Step 2 – Identify Elements
The next step is to identify elements. Record the whole series of steps on video. This will largely help in identifying which steps can be improved.
When each step has been observed, write down the time taken as well as the costs included.
Afterwards, you’ll need to separate out the various elements of the step. Separate them in terms of what can be done by humans, and which are done via machines.
Step 3 – Separate External Elements
For the third step, you’ll need to identify which steps can be done externally. This means it is done before the actual changeover. Include here those steps that you can change from internal to external.
Step 4 – Change Internal Elements to External Elements
Taking from the list from the third step, it is time to analyze those steps that will be changed from internal to external. Identify which of these changed steps would have the biggest positive impact in terms of cost and time.
This will help direct which change of steps can be acted on first.
Step 5 – Start Streamlining
This is the last step where the identified steps are streamlined to make them faster. All elements must be considered.
When streamlining, always take into consideration potential wasted motion and time where people are kept waiting. These two are very important as they are wastes that Lean are trying to address.
Start SMED Now
SMED is another powerful and effective tool that you can use to eliminate waste and increase the efficiency and profitability of your business.
When you put all the steps of SMED together, it will definitely make your business run faster and produce good quality products for your customers. Try out the SMED system for your business now.
You might also wanna check Kanban: A Means to Achieve Just-In-Time Manufacturing.